Implementing Manufacturing Workflow Automation
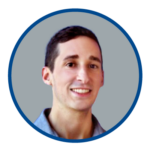
Accelerating Digital Transformation in Life Sciences:
Unlocking Efficiency and Compliance (as seen in MasterControl)
By Anthony DeBiase, Director, Digital PD & Clinical Manufacturing
The life sciences industry faces increasing pressure to streamline operations, ensure compliance, and maintain product quality. Digital transformation in life sciences manufacturing provides an opportunity to address these challenges head on. In a business environment where artificial intelligence (AI) dominates conversation, the life sciences industry cannot take advantage of this transformational technology without implementing core digital systems. Adopting digital systems empowers life sciences organizations to:
- Improve production efficiency
- Meet regulatory standards
- Enhance data integrity
Streamline Workflows, Reduce Errors, and Accelerate Production With Process Automation
Implementing digital systems that provide manufacturing workflow automation can significantly improve production efficiency through the entire production lifecycle for supervisors, operators on the floor, and quality teams.
Life sciences manufacturing takes place in highly controlled process areas where minimizing the number of personnel is a strategy to reduce contamination. This limits the supervisor’s ability to gain real-time insight into manufacturing outside of traditional equipment sensor data. Supervisors must rely on the data that is generated by the manufacturing records, logs, and equipment to understand how well the manufacturing process is running. This data is received after the processing is complete, not allowing for prevention of any issues that arise. For example, in cell therapies, single-use bioprocessing systems are critical to prevent patient cells cross contamination. These systems provide limited online sensor data compared to that of traditional stainless systems. Traditional stainless-steel systems are highly automated with processes that capture all process actions such as when a valve opens and how long a pump is running. This data can be stored in a historian and trended, while most of the manual interactions such as welding tubing, sampling, and solution transfers aren’t captured automatically. If the data from these events is not captured and reviewed in an efficient way supervisors will have limited insight into their plant operations.
Utilizing manufacturing workflow automation allows supervisors to improve product efficiency through the following steps:
- Collect Data: Aggregate all activities (“online” machine automation and “offline” manual procedures)
- Track and Trend: Visualize your personnel and facility constraints in real time
- Control: Debottleneck the process, optimize your production activities, and schedule and reduce downtime
- Maintain: Understand the implications of changes in your manufacturing process
These systems can also provide dashboards that improve operational awareness for operators on the production floor. Operators can leverage data to make informed decisions or navigate complicated processes. A frequent challenge in this space is varying raw or starting patient material quality. Starting cell density or cell growth can vary drastically, causing uncertainty in processing actions to take. Manufacturing workflow automation such as flexible, electronic batch records can build quality and efficiency into the process by guiding operators through these challenges. A digital solution that directly links batch records and work instructions to information such as standard operating procedures (SOPs) and other documents found in a quality management system (QMS) gives operators access to everything they need to successfully execute batches.
Cell therapy processes are very manual and require significant scale out to meet patient demand. Scaling out further exacerbates the challenges of the operations. In addition, labor-intensive paper processes add to the workload of already overburdened operators. Every page of records can have multiple opportunities for human error including incorrect entries, miscalculations, and executing steps out of order. Implementing manufacturing workflow automation such as an electronic batch record in a manufacturing execution system (MES) can eliminate these opportunities for error.
With the appropriate insight into the production floor utilizing manufacturing workflow automation solutions, life sciences manufacturers can move from being reactive to proactive. These tools also allow operators to make guided decisions for complex processes. This provides some key benefits:
- Maintain quality
- Maximize uptime
- Improve throughput
- Reduce waste
- Effectively scale up or out
Implementing Digital Systems to Improve Quality Oversight, Maintain Regulatory Compliance, and Improve Audit Readiness
Maintaining life sciences regulatory compliance is a critical focus for manufacturers in the industry. Digital transformation in life science manufacturing not only helps supervisors and operators increase operational efficiency, but it enhances the capability of quality assurance teams to build and maintain regulatory compliant business processes. Digital systems do this by giving quality teams the data and information they need in a timely and structured manner. Examples include:
- Reducing the risk of manual errors and inconsistencies by enforcing rules that must be followed
- Capturing, investigating, and resolving deviations
- Saving significant review time by preventing simple but consistent good documentation practice (GDP) mistakes such as significant figures
- Reducing review cycles with review by exception
- Tracking corrective action/preventive action (CAPA) effectiveness
- Facilitating continuous process verification (CPV)
Meeting Regulators’ Data Integrity Expectations
In recent years, regulatory agencies have increasingly observed current good manufacturing practice (cGMP) violations involving data integrity during inspections. Upholding data integrity is an important component to ensure the safety, efficacy, and quality of drugs. Maintaining accurate and complete documentation is essential for regulatory audits and inspections.
Manufacturing workflow automation can provide solutions for compliance with 21 CFR Parts 210, 211, and 212, which set forth the following data integrity requirements:
- “backup data are exact and complete,” and “secure from alteration, inadvertent erasures, or loss”
- data be “stored to prevent deterioration or loss”
- certain activities be “documented at the time of performance”
- records be retained as “original records,” “true copies,” or other “accurate reproductions of the original records”
- requiring “complete information,” “complete data derived from all tests,” “complete record of all data,” and “complete records of all tests performed”
Additional Benefits Digital Systems Provide
Other opportunities for companies seeking to maintain life sciences regulatory compliance utilizing digital systems include:
- Facilitate better collaboration and communication across departments and with external partners, including regulatory agencies
- Easily reviewed regularly and updated to reflect the latest regulatory requirements or to meet regulatory requirements in a specific geographic location
- Centralized platform for storing, managing, and accessing data that ensures all data and information is organized, accessible, and secure
- Enable compliant workforce growth by managing employee training records and qualification statuses
By embracing digital transformation in life sciences manufacturing organizations can not only enhance overall operational efficiency but also ensure compliance with regulatory requirements. This holistic approach supports sustained growth and competitiveness in a highly regulated environment. Building this foundation will allow for scalability and ultimately the ability to leverage new and transformational technologies such as AI.
Now that you understand the benefits of implementing digital systems to your manufacturing workflow, please reach out to me with your comments or to start a dialog.